About This Webinar
Zinc and zinc alloy plating is a very energy-intensive production process. Rectifiers as well as heating and cooling of the various baths from cleaning to plating and post-treatment contribute to significant power consumption throughout the plating process.
With a focus on developing sustainable and efficient production processes, Atotech helps electroplaters to significantly reduce energy consumption through highly efficient chemical processes and a broad range of auxiliary equipment tailored to these processes. Thus, Atotech not only contributes to cost-efficient production, but also supports the industry in reducing CO2 emissions.
In this webinar, we will present data-based CO2 savings potential that can be achieved with our plating processes and unique anode technology.
Topics that will be covered in our webinar:
• Carbon neutrality targets in the industry
• Relevant CO2 sources in the plating process and calculation of the resulting emissions
• Reduction possibilities of CO2 emissions in zinc nickel plating
- Alternative processes
- Auxiliary equipment
• Carbon footprint in the entire value chain
• Q&A session
As an innovative and environmentally conscious company, our goal is to be the leading supplier of sustainable surface finishing systems. In all our product lines, we strive to reduce the use of toxic substances and provide production processes that use less water and energy - all while reducing waste and emissions. We are here to help our customers reduce their CO2 emissions already today.
Dr. Matthias Hoch
Global Business Development Manager & Special Projects
Dr. Matthias Hoch, who holds a PhD in Chemistry, has more than 30 years industry experience. In 2011 he joined the Atotech corrosion protection team as Global Business Development Manager & Special Projects focusing on worldwide customer and business partner projects. Dr. Hoch's extensive experience ranges from in-depth market knowledge, product, key account and project management to business development.
IndianSurfaceFinishing.com is a dedicated online forum and resource hub focused on the surface finishing industry, offering insightful blog posts and technical guides on various industrial processes that enhance the properties of manufactured items. Managed with a focus on practical applications and innovations, the platform shares detailed procedures, working parameters, maintenance tips, and product recommendations. Contact us - email to info@excellaboratories.com or info@essesstrading.in
Subscribe to:
Posts (Atom)
Innovations in Sustainable Decorative Plating: Insights from the Surface Coating Expo 2025
The Surface Coating Expo 2025 highlighted advancements in sustainable decorative plating, focusing on chrome-free and PAS-free processes. Ke...
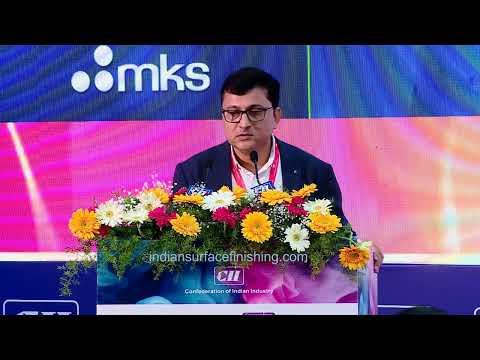
-
HEEF 25 is a fluoride-free hard chromium process that offers high current efficiency. It can be adapted for various applications, includin...
-
This blog post provides a comprehensive overview of Hull Cell panels, including their purpose, the equipment needed for interpretation, a...
-
This blog post provides a detailed guide on how to run a Hull Cell, a miniature electroplating cell used to evaluate electroplating solu...